Jaw Crusher Working Principle
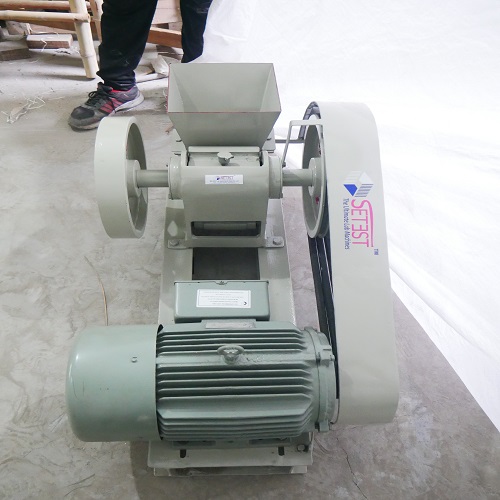
A jaw crusher is a device that is used in an industrial setting to reduce or crush the size of hard materials. Many times, it is not possible for human beings to reduce the size by hammer and other tools. As the name itself suggests, materials are put into the jaw, and it crushes into pieces. Jaws use compressive force to crush solid material like metal items.
Similar to the human jaw, the machine has two parts. One part remains stationary, and the second part move upside down. Workers put the material into the jaw, and the moving part put the compressive strength to crush. In this informative blog, we will discuss all jaw crushers.
What is a jaw crusher?
As the the name itself denotes, It is a device that is used for crushing the size of hard material.
Use of jaw crusher
Businesses order the product from jaw crusher suppliers in Delhi, India and use it for different purposes. In general, case, the following are the main use of jaw crusher-
- Many times, it is not convenient for businesses to carry hard materials from one place to another. Transportation and storage become difficult. Labor also feel difficult to load the material on the transportation medium, in that case, businesses require a jaw crusher.
- Industries need different ore or materials for different sizes to manufacture the ultimate product. To obtain the size and surface area, businesses use a jaw crusher.
- Separation of different minerals from ore, Or separating one ore from another ore is another problem business faces. Get this product from Jaw crusher exporters in Delhi, India and use it for separation purposes.
- At the enrichment stage, the business needs to obtain the size and surface area of the hard materials. Jaw crushers are useful in that case too.
Jaw crushing process
The machine works for different crushing stages. Once a business order the product from a jaw crusher manufacturers in Delhi, India, we deliver at the fastest possible time. Later, the product is used through various processes.
First crushing
This stage is also called the primary crushing process. In that phase, the size of the feeded material gets down to 150 to 300 MM. When the hard material is put into the jaw crusher, the material usually has the primary size of 800 to 1500 MM. The machine reduces it to less than 50 percent of the actual size.
Second crushing
The material comes to this stage after the first crushing process. Here, the material gets reduced to 50 to 80 MM from 150 to 300 MM. If the material size is already between 150 to 300MM, a business may choose the second crushing process directly.
Third crushing or Tertiary crushing
This is the last stage of crushing, The machine reduces the size of material between 5 to 12 MM.
Depending on the requirement of your business, you may choose the crushing process. SE test products are made up to give you complete value for money and once you get the product from jaw crusher manufacturers in Delhi, India, you appreciate the quality and effectiveness of the product.
The working principle of jaw crushers
There is two component of the jaw crusher, Moving side and fixed size. Staff put the material from the top of the machine and ensures that the material is in between the two jaws. Moving side comes and goes however fixed size remains the same. Moving jaw comes and crushes the material. Later, the crushed material is discharged from the bottom of the crusher.
Different components of the jaw crusher
Had you notice there are many parts of the jaw crusher once you receive the product from jaw crusher suppliers in Delhi, India. These are the main components of the jaw crushers.
- Setting and damping group
- Motor stand
- Feed chute
- Drive Flywheel
- Hydraulic cylinder
- Fixed jaw
- Swing jaw
- Toggle place
- Discharge
- Required reduction ration
- Feed Size
- Work index of the ore
- Running cost or capital cost
- Abrasion index
- Compressive strength of the rock
- Consider these facts to enhance the capacity and performance of the jaw crusher.
- Purchase the product from authentic jaw crusher manufacturers and we always advise looking for proper selection of the jaws. Based on your business requirements, choose the product.
- Proper feed rate is also important. This feature ensures that the size of the feed.
- The feed rate of the jaw crusher should be controlled. It means if you have less material to crush, or the staff is not efficient enough, you can control the feed rate.
- The more feeder capacity and width, the more effective product is.
- Enquire about the adequate crusher discharge area before finally sealing the deal with jaw crusher suppliers in Delhi, India.
- It is better to ensure that the discharge conveyor size is maximum as compared to the crusher capacity.
- You should always prefer jaw crushers with High production and reduction.
- The process of installation, operation and maintenance should be easy.
Different type of jaw crushers
jaw crusher manufacturers mainly manufacture two types of products. Even busines demand only two types of product from jaw crusher exporters in Delhi, India.
Singla toggle jaw crusher
This product gets support by the bearing on the eccentric shaft. The shaft is driven by a pitman that is attached. Further, the pitman gets support from the toggle plate of the moveable jaw. When staff runs the machine, the toggle place compresses the hard material between the main body and the moveable jaw. It works on the principle of moving jaw point in an elliptical orbit. The movement ensures that the moveable jaw applies pressure and friction both on the material to crush.
Double toggle jaw crusher
In this type of crusher, the pitman is settled on the non-eccentric shaft. The shaft locates at the top of the crusher. In this type, there are two toggle plates located at the left and right sides. Both the toggle plate are linked with the pitman. Here, the machine applies only pressure to crush the entered material
As a business, you should purchase a double toggle jaw crusher from jaw crusher exporters in Delhi, India. It is ideal for hard and highly abrasive material too. As compared to the single jaw crusher, it is long-lasting. It applies only friction therefore it lasts long. SE test is a number one jaw crusher suppliers of both the type.
Jaw crusher purchasing guide
As a business, you require some information so that you can choose the best jaw crushers. You should consider these factors while ordering or enquiring about the jaw crushers.
.We are hopeful that you have got the best information about jaw crushers. Use this information while purchasing from jaw crusher manufacturers in Delhi, India.